Language of instruction : English |
Exam contract: not possible |
Sequentiality
|
|
Mandatory sequentiality bound on the level of programme components
|
|
|
Group 1 |
|
|
Following programme components must have been included in your study programme in a previous education period
|
|
|
Electrical machines (4061)
|
6.0 stptn |
|
Or group 2 |
|
|
Following programme components must have been included in your study programme in a previous education period
|
|
|
Electrical machines (4061)
|
5.0 stptn |
|
|
| Degree programme | | Study hours | Credits | P2 SBU | P2 SP | 2nd Chance Exam1 | Tolerance2 | Final grade3 | |
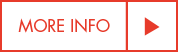 | 3rd year Bachelor Bachelor of Engineering Technology - Electromechanical Engineering Technology - optie design & production | Compulsory | 81 | 3,0 | 81 | 3,0 | Yes | Yes | Numerical |  |
|
| Learning outcomes |
- EC
| EC1 - The holder of the degree possesses general scientific and technological application-oriented knowledge of the basic concepts, structures and coherence of the specific domain. | | - DC
| 1.5 The student knows the basic laws of electrical engineering in the field of electrodynamics and -statics, electromagnetism, one- and three-phase alternating current. | | | - BC
| The student knows the basic electrical machines treated under ELMA (2ba) or TELTS (SCH) and expands this knowledge with the construction, operation and control of the stepper motor and reluctance motor. | | | - BC
| The student knows how a rectifier works and knows the consequences for harmonic pollution. | | | - BC
| The student knows how an inverter works to control an induction motor, BLDC motor, stepper motor and synchronous motor. | | | - BC
| The student knows the operation and implementation of U/f control and FOC (vector control). | | - DC
| EM 1.1 The student has knowledge of signal processing and system modelling. | | | - BC
| The student knows the equivalent scheme of different electrical machines. | | | - BC
| The student knows the different factors that contribute to the efficiency of a system or more specifically to the efficiency of an induction motor. | | - DC
| EM 1.8 The student has advanced knowledge of the key concepts of strength learning and knowledge of the functional operation of common machine parts and mechanisms. | | | - BC
| The student can translate the basic data of a powertrain into torques and speeds for the selection of the desired gearbox and motor for the powertrain. | - EC
| EC2 - The holder of the degree possesses general scientific and discipline-related engineering-technical insight in the basic concepts, methods, conceptual frameworks and interdependent relations of the specific domain. | | - DC
| 2.5 The student understands the basic laws of electrical engineering in the field of electrodynamics and -statics, electromagnetism, one- and three-phase alternating current. | | | - BC
| The student understands the operation and distinction between different types of motors. | | | - BC
| The student can explain and indicate the advantages and disadvantages of U/f or FOC, depending on the application. | | | - BC
| The student understands the difference in implementation between U/f control and FOC and the difference in properties of the controlled system. | | - DC
| EM 2.1 The student has insight into the processing of signals and the modelling of systems. | | | - BC
| The student can translate the measurement data for an induction motor into an equivalent scheme and understands the limitations of this equivalent scheme for modulating this induction motor. | - EC
| EC5 - The holder of the degree can analyse unknown, domain-specific problems, subdivide them, structure them logically, determine the preconditions and interpret the data scientifically. | | - DC
| EM 5.2 The student can analyse an industrial electrical installation and an electrical power train. | | | - BC
| The student is able to select and dimension the power control based on a description and specifications of an electric powertrain. | | - DC
| 5.2 The student can translate application-oriented tasks into a 'known unknown formula' structure. | - EC
| EC6 - The holder of the degree can select and use adequate solution methods to solve unknown, domain-specific problems and can work methodologically and make solid design choices. | | - DC
| EM 6.2 The student can design an industrial electrical installation and an electrical power train. | | | - BC
| The student is able to calculate and dimension the complete electric powertrain based on a selected gearbox, motor and power control. | - EC
| EC7 - The holder of the degree can use the selected methods and tools innovatively to systematically implement domain-specific solutions and designs while being aware of practical and economic conditions and company-related implications. | | - DC
| EM 7.2 The student can validate (parts of) an industrial electrical installation or electric power train using appropriate software tools and implement them in a lab context. | | | - BC
| The student can explain the operation of the power control based on the measurement results | - EC
| EC9 - The holder of the degree can communicate with colleagues in oral and in written form (including in a graphical way) about domain-specific aspects in suited language making use of apt terminology. | | - DC
| 9.1 The student is able to communicate in writing in a correct, structured and appropriate manner in languages relevant to their field of study.
| | | - BC
| The student can correctly display his lab measurements and the processing of these measurement results in a report. | | | - BC
| The student can correctly represent the calculation, dimensioning and control of an electric powertrain in a report and present the relevant results in the conclusion of this report. | - EC
| EC12 - The holder of the degree can act application-oriented and goal-driven and can act academically and professionally with the necessary perseverance and with eye for realism and efficiency, showing a research-oriented attitude towards lifelong learning. | | - DC
| 12.1 The student has an open attitude to learn from experience, feedback and mistakes. | | | - BC
| The student can work on a project basis with an eye for efficiency, practical solutions and does not lose sight of the preconditions (formative, not explicitly evaluated). | | | - BC
| The student can collect correct data through research and is looking for insight into the problem (lifelong learning) (formative, not explicitly evaluated). |
|
| EC = learning outcomes DC = partial outcomes BC = evaluation criteria |
|
The student knows the operation of the transformer, DC motor and induction motor and can draw up the equivalence circuit for these electric machines. The student can calculate the mechanical forces due to friction, weight, acceleration and can translate these forces into potential energy, kinetic energy, mechanical energy and efficiency.
|
|
|
Motivation:
Education in Electric drives is essential in the formation of engineers as it equips them with a systematic approach to navigate the complexity and wide-ranging applications of drive systems. In an era where drive systems are becoming increasingly intricate, including motors, control mechanisms, and system integration, a structured understanding is crucial. This course provides students with the tools and knowledge to analyze, design, and implement drive systems effectively, fostering a systematic mindset applicable across various engineering disciplines.
By emphasizing a systematic approach, the course enables students to identify and address challenges, optimize system efficiency, and ensure reliable operation. Moreover, it prepares them to stay at the forefront of technological advancements in motor technology, power electronics, and control techniques. With this comprehensive understanding, students are well-equipped to make informed decisions, troubleshoot problems, and contribute to ongoing research and innovation in drive systems.
|
Lectures (12 x 2u):
1. Rehearsal ELMA
Industrial applications of electric drives.
Structure and general properties of an electric propulsion system
General aspects of electric drives (structure, motor types, load types, influence of the environment, etc)
Sizing of electric drives
2. Regulated DC drives
Independently excited and permanent magnet DC motor: construction characteristics, etc
Control of a DC motor
Regulated one-quadrant drive, powered from AC mains
Two- and four-quadrant operation, powered from AC mains
Power supply from a DC mains
3. Power conversion in Drives
Power electronics components
Basic circuits for rectification and alternating, DC-DC converters, alternating current choppers.
Power supply units and brake units
Components for determining rotor speed and position
4. AC drives:
Induction machines
- Scalar control: subsynchronous cascade control, U/f control, field weakening
- Derivation and implementation of field orientation and direct torque control (DTC)
Synchronous machine types
- Synchronous machines with emphasis on permanent magnet machines with sinusoidal drive
- Brushless DC machine
- Switched reluctance machine
- Stepper motors
5. Applications
Selection of applications, applied to the resp. machine types: electric transport (hybrid and electric vehicles, trains), electric energy production (variable speed wind turbines), robotics
|
|
|
Period 2 Credits 3,00
Evaluation method | |
|
Written evaluaton during teaching periode | 20 % |
|
Transfer of partial marks within the academic year | ✔ |
|
|
|
Other | Quizzes during classes |
|
|
|
|
|
Written exam | 80 % |
|
|
Multiple-choice questions | ✔ |
|
|
|
|
|
|
Second examination period
Evaluation second examination opportunity different from first examination opprt | |
|
|
|
|
|
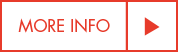 | Bridging programme Electromechanical Engineering Technology optie ontwerp en productie - deel 3 | Compulsory | 81 | 3,0 | 81 | 3,0 | Yes | Yes | Numerical |  |
|
|
|
The student knows the operation of the transformer, DC motor and induction motor and can draw up the equivalence circuit for these electric machines. The student can calculate the mechanical forces due to friction, weight, acceleration and can translate these forces into potential energy, kinetic energy, mechanical energy and efficiency.
|
|
|
Motivation:
Education in Electric drives is essential in the formation of engineers as it equips them with a systematic approach to navigate the complexity and wide-ranging applications of drive systems. In an era where drive systems are becoming increasingly intricate, including motors, control mechanisms, and system integration, a structured understanding is crucial. This course provides students with the tools and knowledge to analyze, design, and implement drive systems effectively, fostering a systematic mindset applicable across various engineering disciplines.
By emphasizing a systematic approach, the course enables students to identify and address challenges, optimize system efficiency, and ensure reliable operation. Moreover, it prepares them to stay at the forefront of technological advancements in motor technology, power electronics, and control techniques. With this comprehensive understanding, students are well-equipped to make informed decisions, troubleshoot problems, and contribute to ongoing research and innovation in drive systems.
|
Lectures (12 x 2u):
1. Rehearsal ELMA
Industrial applications of electric drives.
Structure and general properties of an electric propulsion system
General aspects of electric drives (structure, motor types, load types, influence of the environment, etc)
Sizing of electric drives
2. Regulated DC drives
Independently excited and permanent magnet DC motor: construction characteristics, etc
Control of a DC motor
Regulated one-quadrant drive, powered from AC mains
Two- and four-quadrant operation, powered from AC mains
Power supply from a DC mains
3. Power conversion in Drives
Power electronics components
Basic circuits for rectification and alternating, DC-DC converters, alternating current choppers.
Power supply units and brake units
Components for determining rotor speed and position
4. AC drives:
Induction machines
- Scalar control: subsynchronous cascade control, U/f control, field weakening
- Derivation and implementation of field orientation and direct torque control (DTC)
Synchronous machine types
- Synchronous machines with emphasis on permanent magnet machines with sinusoidal drive
- Brushless DC machine
- Switched reluctance machine
- Stepper motors
5. Applications
Selection of applications, applied to the resp. machine types: electric transport (hybrid and electric vehicles, trains), electric energy production (variable speed wind turbines), robotics
|
|
|
Period 2 Credits 3,00
Evaluation method | |
|
Written evaluaton during teaching periode | 20 % |
|
Transfer of partial marks within the academic year | ✔ |
|
|
|
Other | Quizzes during classes |
|
|
|
|
|
Written exam | 80 % |
|
|
Multiple-choice questions | ✔ |
|
|
|
|
|
|
Second examination period
Evaluation second examination opportunity different from first examination opprt | |
|
|
|
|
|
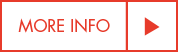 | Exchange Programme Engineering Technology | Optional | 81 | 3,0 | 81 | 3,0 | Yes | Yes | Numerical |  |
|
|
|
Motivation:
Education in Electric drives is essential in the formation of engineers as it equips them with a systematic approach to navigate the complexity and wide-ranging applications of drive systems. In an era where drive systems are becoming increasingly intricate, including motors, control mechanisms, and system integration, a structured understanding is crucial. This course provides students with the tools and knowledge to analyze, design, and implement drive systems effectively, fostering a systematic mindset applicable across various engineering disciplines.
By emphasizing a systematic approach, the course enables students to identify and address challenges, optimize system efficiency, and ensure reliable operation. Moreover, it prepares them to stay at the forefront of technological advancements in motor technology, power electronics, and control techniques. With this comprehensive understanding, students are well-equipped to make informed decisions, troubleshoot problems, and contribute to ongoing research and innovation in drive systems.
|
Lectures (12 x 2u):
1. Rehearsal ELMA
Industrial applications of electric drives.
Structure and general properties of an electric propulsion system
General aspects of electric drives (structure, motor types, load types, influence of the environment, etc)
Sizing of electric drives
2. Regulated DC drives
Independently excited and permanent magnet DC motor: construction characteristics, etc
Control of a DC motor
Regulated one-quadrant drive, powered from AC mains
Two- and four-quadrant operation, powered from AC mains
Power supply from a DC mains
3. Power conversion in Drives
Power electronics components
Basic circuits for rectification and alternating, DC-DC converters, alternating current choppers.
Power supply units and brake units
Components for determining rotor speed and position
4. AC drives:
Induction machines
- Scalar control: subsynchronous cascade control, U/f control, field weakening
- Derivation and implementation of field orientation and direct torque control (DTC)
Synchronous machine types
- Synchronous machines with emphasis on permanent magnet machines with sinusoidal drive
- Brushless DC machine
- Switched reluctance machine
- Stepper motors
5. Applications
Selection of applications, applied to the resp. machine types: electric transport (hybrid and electric vehicles, trains), electric energy production (variable speed wind turbines), robotics
|
|
|
Period 2 Credits 3,00
Evaluation method | |
|
Written evaluaton during teaching periode | 20 % |
|
Other | Quizzes during classes |
|
|
|
|
|
Written exam | 80 % |
|
|
Multiple-choice questions | ✔ |
|
|
|
|
|
|
Second examination period
Evaluation second examination opportunity different from first examination opprt | |
|
|
|
|
|
1 Education, Examination and Legal Position Regulations art.12.2, section 2. |
2 Education, Examination and Legal Position Regulations art.16.9, section 2. |
3 Education, Examination and Legal Position Regulations art.15.1, section 3.
|
Legend |
SBU : course load | SP : ECTS | N : Dutch | E : English |
|